CARBURETORS: CARTER
With the hand throttle lever on the dash set in the closed or off
position, set the throttle lever adjusting screw so that the
engine will run about 300 revolutions per minute with the spark
fully retarded.
A method of determining the speed of the engine when idling is
to grasp one of the valve lifters between the thumb and finger
and count the number of times the valve lifts in twelve seconds.
Multiply this number by ten and the result is the number of revolutions
the engine is turning over per minute.
If the engine runs too fast, back the adjusting screw out slightly
and, if the engine is running too slow, turn in or to the right
until the proper speed is obtained.
Float level: Refer to Fig. 2, where the method of determining the
proper float level is illustrated.
Remove the carburetor bowl and invert the carburetor, then measure
the distance at the point shown, bending the float lever lip slightly
when necessary to get the float to take a position exactly A of
an inch from top of float to machined surface of casting, when
needle is closed.
Fig. 2. Method of locating and adjusting Carter "RXO" float
level, as explained in text. This measurement should be taken on
the side of float opposite gasoline intake needle, using steel
scale and measuring from machined surface of casting, as shown.
Make certain scale does not rest on gasket, or unmachin_ed surface
of carburetor body. If for any reason float lever must be reset,
it may be done by bending float lever lip that conies in contact
with gasoline intake needle. Bending lip up will lower float level
and bending it down will raise it. Only a very slight bend is necessary.
Gasoline strainer: Gasoline enters the carburetor through a fine
wire gauze strainer located in the strainer cap. This strainer
prevents coarse particles of dirt or lint from entering the carburetor
bowl.
The strainer should be removed and cleaned
every 2,000 miles.
To clean the strainer, disconnect the gasoline line and unscrew
the strainer cap screw and lift the strainer cap. Remove the gauze
and clean thoroughly by washing in gasoline and blowing through
it with compressed air. Clean the inside of the strainer cap thoroughly
and reassemble, making sure the gaskets are in place at both ends
of the strainer cap and that the strainer cap screw and gasoline
line are properly tightened and do not leak.
To clean carburetor: The carburetor bowl should be cleaned every
:i 000 miles. Unscrew body and bowl connecting nut and gasket assembly.
Bowl may then be removed and washed in gasoline. Re-move all particles
of lint from the inside.
When reassembling, make certain bowl ring gasket is smooth and
in place on machined surface of body casting before replacing bowl.
Also make certain that body and bowl connecting nut gasket is not
torn and is in proper place, then tighten nuts securely.
Flooding may be caused by dirt lodging between the needle valve
and needle valve-seat, and can sometimes be remedied by tapping
the strainer cap screw, the jar dislodging the dirt and allowing
needle valve to seat.
If this does not remedy the trouble, the needle valve and needle
valve scat should be removed by applying a wrench to the hexagon
needle valve seat just below the strainer cap.
Remove strainer assembly, being careful not to damage any of the
parts or to scratch the polished point of the needle valve or the
needle valve seat. After removing this part wipe off the needle
valve and wash the needle valve seat in gasoline.
The needle valve may then be re-seated if necessary by rotating
it against the needle valve seat and tapping it lightly with the
wooden handle of a hammer or screw driver. It is better to use
wood so as not to damage the face of the needle valve which operates
against the float lever lip.
When replacing, be sure that all parts are properly assembled,
putting the pointed end of the needle valve next to the needle
valve seat, and that all joints in the gasoline lines are tight.
Flooding may also result from the float touching the bowl. This
is caused either by the bowl being improperly seated at the top
or by the float having been damaged. If the float is rubbing, a
bright spot will be found at the point of contact. This may be
corrected by setting the float at its proper level, see Fig. 3,
or seating the bowl on the gasket.
A leaky float will also cause the carburetor to flood. If the float
is leaking it will be evident from its weight and from gasoline
inside of it.
In case of a leaky float, replacement with a new one is the only
practical method, though it is possible to solder a leaking float;
but there is danger of getting too much solder on the float, thus
changing the gasoline level.
When installing a new float, set float level properly as shown
in Fig. 2.
Chevrolet Series "V" Troubles and Remedies
(Carburation) Hard starting: First check up the "choke" hook up, making
sure that the choke valve (Fig. 2) opens and closes properly. Also
look for air leaks in the gasoline system and for plugged or dirty
jets.
Engine slow to warm up: Partly cover radiator in cold weather.
Be sure hot air tube is in place and is not troken or restricted.
The radiator cover is recommended in cold weather.
Poor acceleration may be caused by gaps in spark plugs being too
wide (the proper spark gap for the Chevrolet is .030" or slightly
less than dirt in carburetor, gasoline strainer or air leak in
vacuum tank or gasoline lines.
A new car having a "stiff" engine may also show slow
pick-up or acceleration. Check the engine valves carefully, making
sure none are "riding" or sticking. Be sure compression
is good.
Previous page 1927
Supplement Home Next page 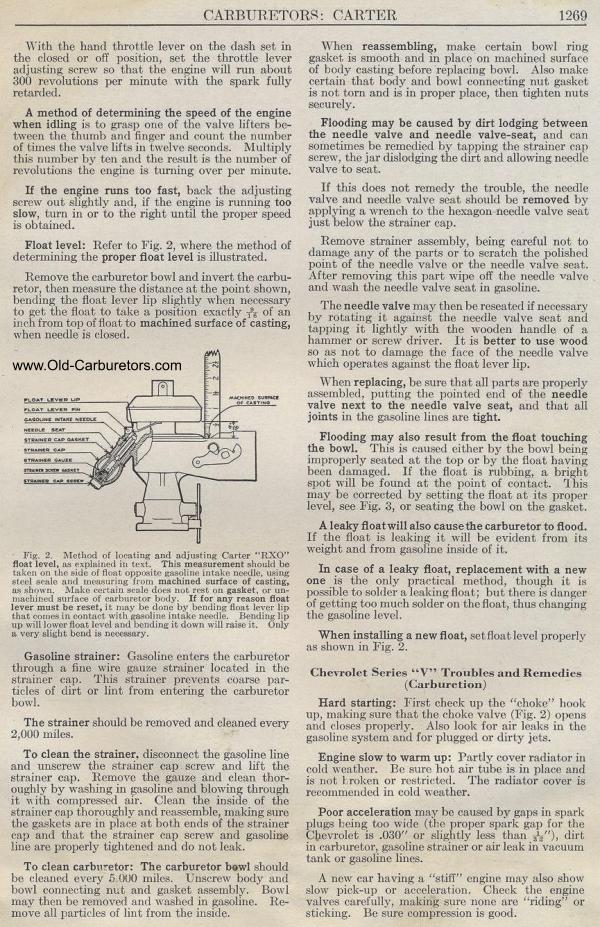 |