Crankshaft Alignment
A surface plate, two A'-blocks, and a dial indicator (G) are used,
the button (C) of the latter being in contact with the center main
bearing journal of 3, 5, 7, or 0 bearing shaft or on the two center
journals in the case of a 4-bearing shaft.
Fig. 24. Surface plate and V-block for crankshaft testing. This
method is recommended for testing the crankshaft for alignment
by setting the shaft so that the front and rear main journals rest
on V-blocks (A).
Swinging the crankshaft between centers on the lathe is not dependable,
because the shaft center holes are often eccentric with the end
journals.
The amount of deflection of the dial gauge divided by two indicates
the amount that the shaft is bent.
If the gauge shows a deflection of .005", or more, the shaft
should be straightened on a suitable press.
It will now be apparent why the test for roundness of journals
should be made before the crankshaft alignment test. When the V-blocks
are used, the shaft is being rotated on its own journals, and if
they are out of round the mechanic would not know whether the deflection
of the dial gauge hand indicated the amount by which the shaft
was sprung, or eccentric rotation of the shaft due to the onn of
round condition, or to the eccentricity of the journal contacting
with the gauge or a combination of all three. Another advantage
in making the check for trueness first is that if this test shows
the pins or journals to be out of round by all amount sufficient
to require regrinding the mechanic need not then trouble about
making further inspection, as the regrinder can make such additional
tests and corrections as may be necessary.
As previously stated, no bearing fitting or renewal should be attempted
until the crankshaft had been tested for straightness and straightened
if necessary and not until all crankpins and journals are brought
to roundness and smoothness.
Assuming the crankshaft then to be in satisfactory condition at
all points mentioned, the mechanic is ready to proceed with the
job of refitting or renewing the main bearings.
First Step in Renewing Main Bearings
The first and most necessary step is not the fitting of the bearings
to the crank journals, but the fitting of the bearings into the
caps and saddles which retain them. lnfitting the wain bearing
halves into their seats the same standards of protrusion, etc.,
as mentioned on a preceding page, should be followed.
The surfaces of the new hearings should be examined as should the
surfaces of the hearing caps and saddles in the blocks for any
foreign matter which might prevent a proper seating.
Each half bearing should be spread slightly wider at the split
edges than the diameter of the cap or saddle into which it is to
fit.
In other words, the bearings should not fit easily or loosely into
their receptacles but should require pressure such as is applied
when the caps and bolts are tightened down, to force the halves
to seat into the caps and saddles.
Most bearings are made this way, but in cases where they do not
fit with some pressure, they should be laid with the split edges
down on the surface plate and struck a few blows carefully on the
back with a soft mallet (Fig. 25).
Fig. 25 (left). Bearing bronze-back, babbitt-lined type) is spread
by a light blow with a wood-en mallet.
Fig. 25A (right). This method of seating the back of bearing is
used on die-cast type backless bearings.
Fig. 28B. The instruction book of the Taft-Pierce service
reamer reads: "Assembling new bearings in crank case: If the
crankshaft has been ground, but not to exceed .020," standard
bearings can usually be fitted. If the shaft has been reduced more
than this amount, use undersize bearings. Thoroughly clean the
bore of the caps and the bearing receiving holes in the crank case
and insert the bearings.
Hammer them in solidly, using hard woad block with the end that
rests in the bearing formed to approximately the same radius as
the bearing and of practically the same length.
File the edges of the cap bearings flush
with the cap. File the edges of the bearings in the case not quite
flush, letting then[ project about .002" or .003" above
the case as nearly as may be determined.
This is done in order that when the cap is assembled the bearings
will come together with a little harder contact than the cap and
case, thereby tending to hold the bearings more securely."
Testing for Protrusion
The next step is to fit the bearing halves into the caps and saddles.
The split edges of the bearing halves in the ease saddles should
protrude from .0005" to .002", as illustrated at Fig.
26.
This protrusion which is sometimes overlooked is recommended by
the largest manufacturers of crank-shaft bearings, as being the
only satisfactory method to insure that the bearings are firmly
seated in their receptacles.
A set of bushings (B) made from brass or steel tubing may be used,
as shown in Fig. 26, to force each bearing half firmly into its
scat while it is examined to see that the proper amount of protrusion
is present.
Fig. 26. The retaining bushings (B) are kept in place (luring fitting
of upper half bearings. The bushings (B) can be made of sawed-off
pieces of seamless steel tubing or discarded bushings of the pro-per
dimensions.
Fig. 26A (lower left). This illustration shows another view of
the bushings (B) to hold bearing down when using hand scraping
method (recommended by Federal Mogul Corpn.) and also
shows spotting from the Prussian blue on babbitt surface of bearing.
As indicated the spotting shows that shaft s almost fully bottomed.
The white part indicates part of bearing which is still too low;
further scraping is necessary.
if each bearing when held tightly into its saddle by the pressure
of the bolts and bushings, as indicated at Fig. 26, can be felt
with the finger nail to be protruding slightly, it may be considered
satisfactory for all ordinary purposes.
When each bearing has been thus tested, the mechanic can proceed
to the job of scraping or reaming, depending upon the equipment
at hand.
Align reaming is beyond doubt the quickest and most accurate method
of fittings the main bearings due, among other advantages, to the
fact that during the reaming process, the main bearing caps are
bolted down tightly as they would be in service.
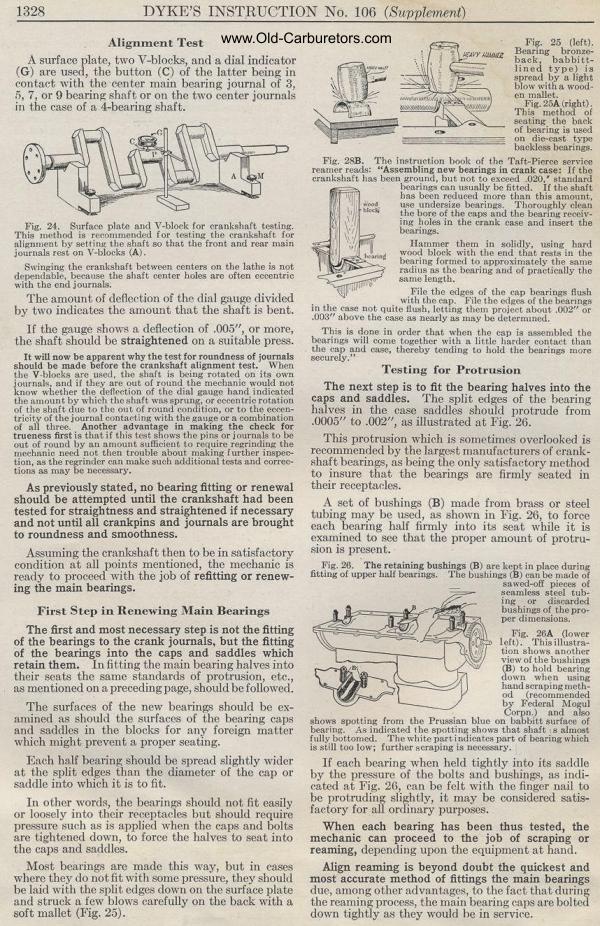 |