Supercharger
One of the simplest types of superchargers is the mechanically
driven centrifugal type as used last year by the Duesenberg race
cars (1924) and (1925) and laid out by David Gregg of McCook
Field, Dayton; this is shown in Fig. 4.'
Fig. 4. The Gregg supercharger, a
mechanically driven centrifugal type.
This supercharger was designed by the
same engineer who developed the super-E charger for the Duesenberg cars, and is manufactured by Green Engineering Works, Dayton, Ohio.
It may be used either to force air into the carburetor under pressure,
or with the carburetor attached to the supercharger inlet.
A It is claimed that this supercharger will add 30 per cent to
the power of the engine. It acts not only as a compressor, but
as a mechanical fuel mixer as well. The churning action of the
impeller (I) mixes the fuel.
The impeller (I) operates at seven times engine speed, accomplished
by the gear step-up (G and H). It maintains a pressure of six to
seven pounds in the intake manifold. In other words, the gas mixture
is forced into the cylinders under pressure of six to seven pounds.
It is usually installed on the front of the car and is driven directly
off the crankshaft by means of a shaft and universal joint attached
to the crank-shaft and supercharger.
The carburetor is connected to the supercharger inlet (A), and
all gas and air from the carburetor passes directly into the supercharger
and is immediately compressed into the cylinders.
Lubrication is accomplished by filling the gear casing (B) through
oil intake (C). The gear casing is filled with fresh oil at the
start of each race. There are no other parts that require lubrication
or attention of any kind. After the race, the oil is drained through
oil drain (D).
The manifold from the supercharger to the intake ports of the engine
is connected to supercharger exhaust (E).
The carburetor throttle varies the amount of supercharging; there
are no valves or pressure regulators to cause trouble. Acceleration
instantly follows a pressure on the throttle, as the supercharger
forces the vaporized mixtur%into the cylinders under pressure.
In this layout the supercharger is placed between the engine and
carburetor, the blower unit being on the left side of the engine
and parallel to it. The shaft of the blower extends through the
engine between the fourth and fifth cylinders and a set of bevel
gears is fitted to take the drive from the end of the water pump
shaft.
The blower revolves at approximately eight times camshaft speed,
the step-up being accomplished by a planetary set of gears. W hen
it is recalled that these engines are capable of turning ov r at
better than 5,000 r. p. m., the speed of the su r-charger becomes
apparent. 777///
The pressure on the charge is about two atmospheres (one atmosphere
being about 14.7 lbs. to the square inch). It takes about two or
three horse-power to drive the supercharger.
It will be readily seen that it is possible to place the supercharger
either ahead or back of the carburetor, by which is meant between
the engine and carburetor or allowing the carburetor to remain
in its normal position and forcing the compressed air through it.
The location of the supercharger does not make a great deal of
difference—with the exception of the fuel feed. When the
supercharger is placed between the engine and carburetor there
is no need for "balancing" the float chamber of the carburetor,
as must be done when the blower is so arranged that the compressed
air is forced through the carburetor air intake.
Under Atmospheric Pressure
With the blower between engine and carburetor the air intake of
the carburetor and fuel in the bowl are under atmospheric pressure
and there will be a constancy of mixture proportion as with a conventional
engine not supercharged.
The disadvantage of the location between engine and carburetor
lies in the fact that a serious explosion might occur in case of
a back-fire.
When the carburetor is placed ahead of the blower it is necessary
to provide an equalizing pressure tube between the fuel in the
carburetor bowl and the carburetor air intake.
The float chamber must be air-tight and kept at a pressure higher
than atmospheric. Since the fuel will not flow into the bowl by
gravity, pressure must also be provided for it.
Automotive Electrical Engineer of July, 1925, prints a very interesting
story on superchargers,' a part of which refers to the views of
Dr. Sandford Moss of the General Electric Co., who did much of
the development work on the superchargers used on the Duesenbergs
in 1925 and who has done much with supercharger design and development
as applied to the automobile. His statements tell plainly the reason
why these new devices can well be expected to develop for use in
the passenger car field. He further states that passenger automobile
requirements differ greatly from those of an airplane engine, a
Deisel engine, or a racing auto engine.
He traces the use of superchargers in internal combustion engines,
pointing out that they have been in use for years on various types
of power plants.
Their use on'airplanes led to the experiments now being made with
automobiles. On airplanes, the supercharger centrifugal compressor
compresses the air from the low density of high altitude to sea-level
density and so supplies the engine with exactly the same charge
as it would receive were it at sea level.
In the same story Mr. David Gregg, research engineer of the L.S.
Air Service at McCook Field, Dayton, Ohio, who has conducted many
of the government tests and is also a pioneer in the work, tells
how a complete redesign of ignition systems will be necessary if
the supercharger is adapted to passenger or commercial car use.
A part of the article reads as follows:
"The limit of present airplane magnetos on a supercharged engine
is about 20,000 feet. Delco ignition, which has larger air gap insulations,
has operated successfully to higher than 35,000 feet. With a supercharged
automobile engine the problem is nearly the same. In this case, instead
of the atmospheric pressure around the magneto or distributor decreasing,
the supercharger increases the pressure in the cylinder and hence
the resistance across the spark plug.
"As the voltage varies with the resistance, this will soon be`a
factor in ignition design, as supercharger pressures of 10 pounds
per square inch are now in use. In designing ignition apparaths for
supercharged engines, air gap insulations should be replaced wherever
possible by insulating material, and the spacing of contact points,
etc., should be great enough to prevent leakage of current at high
voltage.
"To sum up, the ignition system for a supercharged engine should
have a higher voltage than that for the ordinary engine. The spark
plugs should be selected for their cooling capacity and ability to
stand extreme temperature and pressure, and air gap insulation should
be replaced by dielectric material wherever possible."
Not from Motor Age. Addition made by the author.
Fig. 4
<
Previous page 1927
Supplement Home Next page 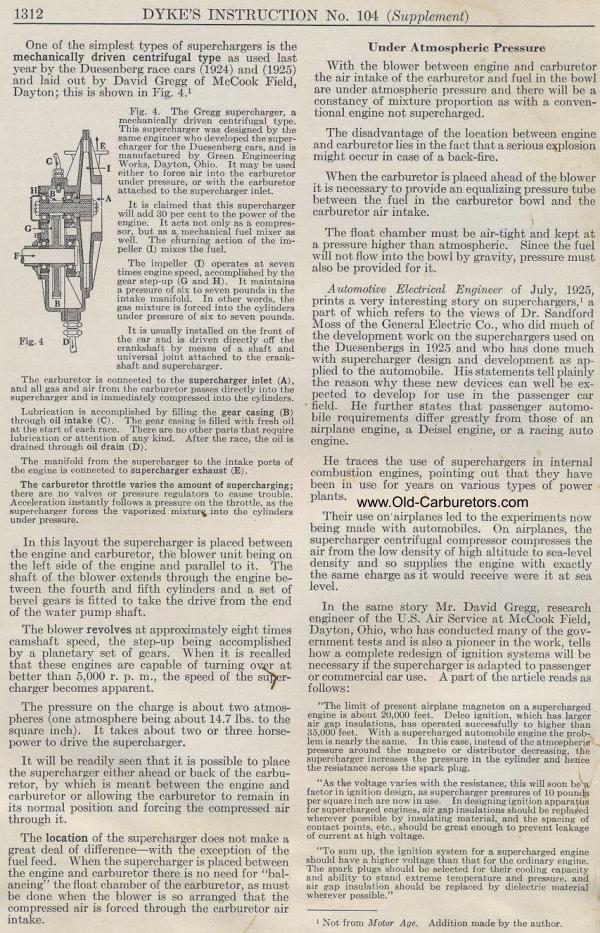 |