Engine Bearings
That is why we advise one carefully to mark all caps before removing
them, not only to indicate the numerical position of the cap,
but also to show which side is nearest to or farthest from the
crankshaft.
Bearing clearances. A little clearance should be provided between
the crank pins and journals and bearing walls on pressure-lubricated
jobs for relief of pressure and maintenance of oil film. This should
not exceed .001" for each inch of crankpin or journal diameter.
Aligning reamers. The best type for accuracy are those which are
set up so that a pilot or some other arrangement guides the reamer
or boring tool in a straight line without permitting any deflection.
Where a plain reaming tool is put through withoutbeing held rigidly
to a predetermined line, it is likely to follow the line of least
resistance, i.e., the path of least contact through the bearings,
springing away from the high spots if necessary, to do this.
End-thrust clearance. Certain main bearings are more subjected
to end thrust wear than others and soon become worn at the flanges,
causing noise. Replacement with new bearings i3 the only remedy.
Most of the new main hearings are provided with a slight extra
amount of stock on the bearing flanges to provide for fitting.
When it is found necessary to remove stock from the flange faces
for fitting, care should be taken to keep the faces square with
the bearing holes.
EXAMPLE OF A PRESSURE LUBRICATED MAIN BEARING LAYOUT
Example of a typical crankshaft main bearing lay-out is shown in
Fig. 28.
The crank case is shown up-side-down to expose the upper crankshaft
main bearing halves which are shown in the saddles or seats of
the crankcase.
Fig. 28 The Nash advanced six engine, series 261 bearings.
The crankshaft has seven main bearings 2%" in diameter. The
length of the front (FB) and rear (RB) bearings is 2 11/16",
and of the four intermediate bearings Nos. 2, 3, 5, and 6, 1 3/16",
and of the center bearing, No. 4, 2".
The end thrust of the crankshaft is carried against flanges (F)
on the center bearing where an end clearance of .005" must
exist.
The bearings are bronze shells lined with babbitt, termed "bronze
- backed babbitt-lined bearings," and secured in the crankcase
and caps with screws.
When caps are removed for bearing adjustments, they must be replaced
in the original position to insure alignment of the oil grooves.
Reversing a bearing cap closes the oil passage to the camshaft,
and limits the supply to the connecting rods and cylinders.
The bearing caps are shown in Figs. 1, 2, 3, 4, 5, 6, and 7 below
the crankcase, and when drilled crankshaft is placed in the upper
half bearings the caps containing their bearings are placed over
the crankshaft and bolted in place.
Between each bearing cap and the case are shims, two on each side,
a total of .004" in thickness. The removal of one or two shims
will usually suffice for an adjustment of the bearings after considerable
service.
If a further reduction of clearance is necessary, the bearing
cap should be evenly filed or reduced by applying it to a sheet
of emery cloth placed on a surface plate.
Crankshaft main bearings should be adjusted to approximately .002" clearance.
The shaft should rotate freely when turned by hand.
Oil distributor line from oil pump connects under each bearing
cap and oil passes through holes (D). Semi annular grooves convey
oil from the distributor manifold connections in the bearing caps
to a point near the top of the upper half of bearings in crank
case where oil ducts (C) in bearings 2, 3, 5, and 7 which are integral
with the crankcase, convey oil to the camshaft bearings.
Oil shedders (0), (Fig. 9) serve to prevent the leakage of oil
from the rear bearings and another is at front for the frontbearings.
The edge of the rear bearing cap at point 01 (Fig. 28) should fit
the crankshaft with a clearance of .012". The con-tour of
the bearing cap at this point must be altered whenever the bearing
is adjusted by the removal of shims or by filing the cap.
Fig. 29. Piston and connecting rod. Name of parts 1, 2, 4, plain
rings; 3, oil-regulating ring; 5, piston pin; 6, piston-pin lock
screw; 7, piston-pin bushing; 8, connecting-rod oil holes; 9, connecting-rod
adjusting shims; two .002" shims on each side; 10, connecting-rod
bolt, nut, and cotter.
Note the oil holes (8) in the connecting rod. The purpose of these
oil holes is to lubricate the cylinders, pistons and pins explained
as follows: At each revolution of the crankshaft, holes drilled
in the crankshaft extending from the main bearings to the connecting-rod
bearings coincide with the oil-entrance grooves in the main bearing
caps and conduct oil to the connecting-rod bearings.
The cylinders and pistons are lubricated by streams of oil intermittently
ejected from the crankshaft through these holes (8) in the connecting
rods. The ejecting occurs only when the piston is at the top of
its stroke. This is especially desirable when starting, after a
car has stood for a long while and oil has drained from cylinder
walls. This also supplies a spray of oil for lubricating the cams
and tappets.
To check the flow of oil through the connecting rods, the crankshaft
should be turned until each piston is at the top of the stroke,
and while in this position an air hose should be attached to the
oil pump connection of the distribution manifold.
If the opening and oil tubes are clear, oil will be forced through
the shaft and out of the holes in the connecting rod.
The pistons are light iron, each provided with four rings.
The third ring is an oil regulator, and a number of holes are drilled
from the third groove to the inside of the piston.
All rings should fit the grooves with a clearance not to exceed
.002".
The piston pin is retained in the piston by a lock screw secured
with a i ek washer and a cotter pin.
Piste as, rings, and pins should be removed for inspection each
1Q,000 miles.
If the piston pins or the connecting-rod bushings are worn, they
may be replaced.
Oversize piston pins should not be used as it is impossible accurately
to re-ream the hole in the pistons.
Previous page 1927
Supplement Home Next page 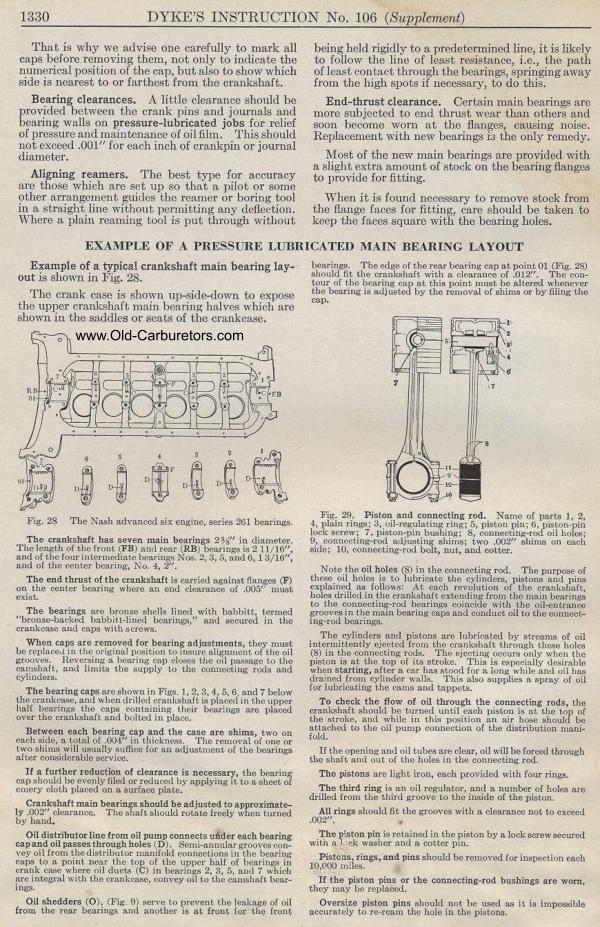 |