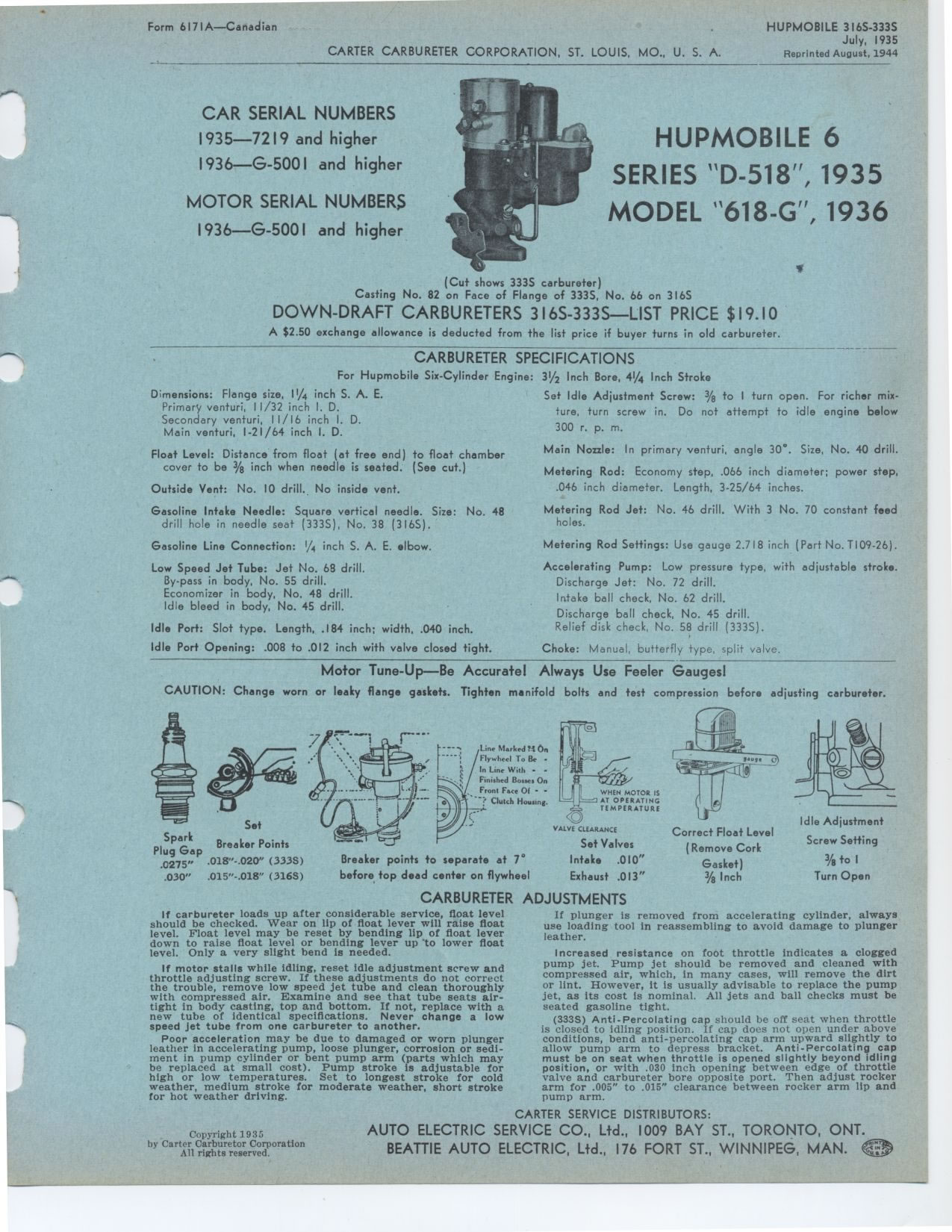
CARTER CARBURETER CORPORATION, ST. LOUIS, MO., U. S. A.
Form 6171A—Canadian
HUPMOBILE 316S 333S
July, 1935
Reprinted August, 1944
CAR SERIAL NUMBERS 1935—7219 and higher 1936—G-5001 and higher
MOTOR SERIAL NUMBERS 1936—G-5001 and higher
HUPMOBILE 6
SERIES D-518, 1935
MODEL 618-G, 1936
(Cut shows 333S carbureter)
Casting No. 82 on Face of Flange of 333S, No. 66 on 316S
DOWN-DRAFT CARBURETERS 316S-333S—LIST PRICE $19.10
A $2.50 exchange allowance is deducted from the list price if buyer turns
in old carbureter.
CARBURETER SPECIFICATIONS
For Hupmobile Six-Cylinder Engine:
Dimensions: Flange size, 11/4 inch S. A. E. Primary venturi, 11/32
inch I. D.
Secondary venturi, 11/16 inch I. D. Main venturi, 1-21/64 inch I. D.
Float Level: Distance from float (at free end) to float chamber cover
to be 3/8 inch when needle is seated. (See cut.)
Outside Vent: No. 10 drill. No inside vent.
Gasoline Intake Needle: Square vertical needle. Size: No. 48 drill
hole in needle seat (333S), No. 38 (316S).
Gasoline Line Connection: 1/4 inch S. A. E. elbow.
Low Speed Jet Tube: Jet No. 68 drill. By-pass in body, No. 55 drill.
Economizer in body, No. 48 drill. Idle bleed in body, No. 45 drill.
Idle Port: Slot type. Length, .184 inch; width, .040 inch. Idle Port
Opening: .008 to .012 inch with valve closed tight.
31/2 Inch Bore, 4¼ Inch Stroke
Set Idle Adjustment Screw: % to I turn open. For richer mixture, turn
screw in. Do not attempt to idle engine below 300 r. p. m.
Main Nozzle: In primary venturi, angle 30°. Size, No. 40 drill. Metering
Rod: Economy step, .066 inch diameter; power step, .046 inch diameter. Length,
3-25/64 inches.
Metering Rod Jet: No. 46 drill. With 3 No. 70 constant feed holes.
Metering Rod Settings: Use gauge 2.718 inch (Part No. T109-26). Accelerating
Pump: Low pressure type, with adjustable stroke. Discharge Jet: No.
72 drill.
Intake ball check, No. 62 drill.
Discharge ball check, No. 45 drill. Relief disk check, No. 58 drill
(3335).
Choke: Manual, butterfly type, split valve.
Motor Tune-Up--Be Accurate! Always Use Feeler Gauges!
CAUTION: Change worn or leaky flange gaskets. Tighten manifold bolts and
test compression before adjusting carburetor.
Line Marled M On Flywheel To Be - In Line With - - Finished Bosses On Front
Face Of - -
Clutch Housing.
Set
Spark
Plug Gap Breaker Points
M75r. .018"-.020" (333S) .030" .015"-.015" (316S)
Breaker points to separate at 7° before top dead center on flywheel
VALVE CLEARANCE
Set Valves Intake .010" Exhaust .013"
Correct Float Level
( Remove Cork
Gasket) 3/g Inch
Idle Adjustment
Screw Setting
% to I
Turn Open
CARBURETER
If carbureter loads up after considerable service, float level should be
checked. Wear on lip of float lever will raise float level. Float level may
be reset by bending lip of float lever down to raise float level or bending
lever up to lower float level. Only a very slight bend is needed.
If motor stalls while idling, reset idle adjustment screw and throttle adjusting
screw. If these adjustments do not correct the trouble, remove low speed
jet tube and clean thoroughly with compressed air. Examine and see that tube
seats air-tight in body casting, top and bottom. If not, replace with a new
tube of identical specifications. Never change a low speed Jet tube from
one earbureter to another.
Poor acceleration may be due to damaged or worn plunger leather in accelerating
pump, loose plunger, corrosion or sediment in pump cylinder or bent pump
arm (parts which may be replaced at small cost). Pump stroke is adjustable
for high or low temperatures. Set to longest stroke for cold weather, medium
stroke for moderate weather, short stroke for hot weather driving.
ADJUSTMENTS
If plunger is removed from accelerating cylinder, always use loading tool
in reassembling to avoid damage to plunger leather.
Increased resistance on foot throttle indicates a clogged pump jet. Pump
jet should be removed and cleaned with compressed air, which, in many cases,
will remove the dirt or lint. However, it is usually advisable to replace
the pump jet, as its cost is nominal. All Jets and ball checks must be seated
gasoline tight.
(333S) Anti-Percolating cap should be off seat when throttle is closed to
idling position. If cap does not open under above conditions, bend anti-percolating
cap arm upward slightly to allow pump arm to depress bracket. Anti-Percolating
cap must be on seat when throttle is opened slightly beyond idling position,
or with .030 inch opening between edge of throttle valve and carbureter bore
opposite port. Then adjust rocker arm for .005" to .015" clearance
between rocker arm lip and pump arm.
Copyright 1935
|