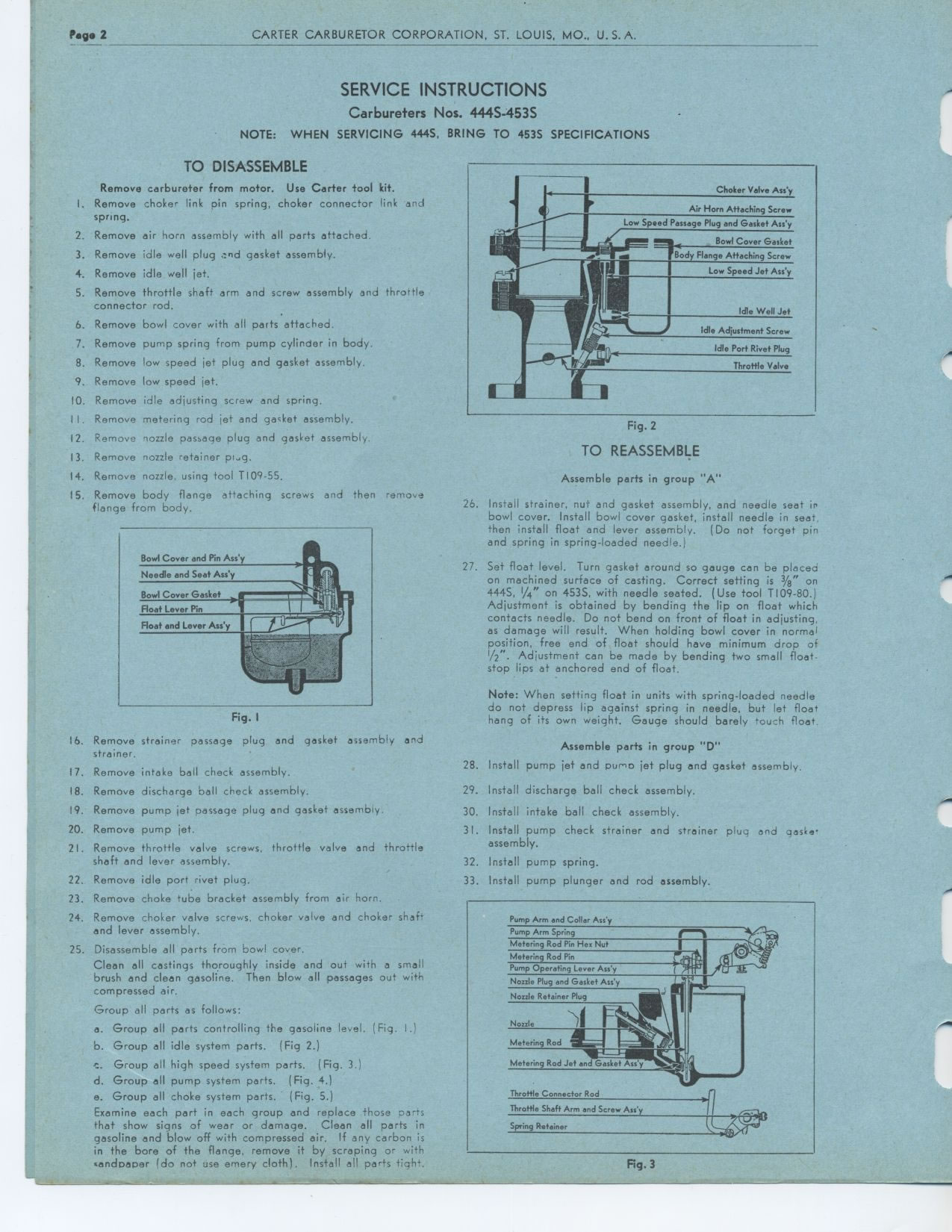
Pogo 2 CARTER CARBURETOR CORPORATION, ST. LOUIS, MO., U.S.A.
SERVICE INSTRUCTIONS
Carburetors Nos. 444S-453S
NOTE: WHEN SERVICING 4445, BRING TO 453S SPECIFICATIONS
TO DISASSEMBLE
Remove carbureter from motor. Use Carter tool kit.
1. Remove choker link pin spring, choker connector link and spring.
2. Remove air horn assembly with all parts attached.
3. Remove idle well plug and gasket assembly.
4. Remove idle well jet.
5. Remove throttle shaft arm and screw assembly and throttle connector rod.
b. Remove bowl cover with all parts attached.
7. Remove pump spring from pump cylinder in body.
8. Remove low speed jet plug and gasket assembly.
9. Remove low speed jet.
10. Remove idle adjusting screw and spring. I I. Remove metering rod jet
and gasket assembly.
12. Remove nozzle passage plug and gasket assembly.
13. Remove nozzle retainer pi„g.
14. Remove nozzle, using tool T109-55.
15. Remove body flange attaching screws and then remove flange from body.
Fig. I
lb. Remove strainer passage plug and gasket assembly and strainer.
17. Remove intake ball check assembly.
18. Remove discharge ball check assembly.
19. Remove pump jet passage plug and gasket assembly.
20. Remove pump jet.
21. Remove throttle valve screws, throttle valve and throttle shaft and lever
assembly.
22. Remove idle port rivet plug.
23. Remove choke tube bracket assembly from air horn.
24. Remove choker valve screws, choker valve and choker shaft and lever assembly.
25. Disassemble all parts from bowl cover.
Clean all castings thoroughly inside and out with a small brush and clean
gasoline. Then blow all passages out with compressed air.
Group all parts as follows:
a. Group all parts controlling the gasoline level. (Fig . 1.)
b. Group all idle system parts. (Fig 2.)
as. Group all high speed system parts. (Fig. 3.)
d. Group all pump system parts. (Fig. 4.)
e. Group all choke system parts. (Fig. 5.)
Examine each part in each group and replace those parts that show signs of
wear or damage. Clean all parts in gasoline and blow off with compressed
air. If any carbon is in the bore of the flange, remove it by scraping or
with sandpaper (do not use emery cloth). Install all parts tight.
Fig. 2
TO REASSEMBLE
Assemble parts in group "A"
26. Install strainer, nut and gasket assembly, and needle seat it bowl cover.
Install bowl cover gasket, install needle in seat, then install float and
lever assembly. (Do not forget pin and spring in spring-loaded needle.)
27. Set float level. Turn gasket around so gauge can be placed on machined
surface of casting. Correct setting is 3/8" on 444S, 1/4" on 453S,
with needle seated. (Use tool T109-80.) Adjustment is obtained by bending
the lip on float which contacts needle. Do not bend on front of float in
adjusting, as damage will result. When holding bowl cover in normal position,
free end of float should have minimum drop of 1/2". Adjustment can be
made by bending two small float-stop lips at anchored end of float.
Note: When setting float in units with spring-loaded needle do not depress
lip against spring in needle, but let float hang of its own weight. Gauge
should barely touch float.
Assemble parts in group "D"
28. Install pump jet and pu!wo jet plug and gasket assembly.
29. Install discharge ball check assembly.
30. Install intake ball check assembly.
31. Install pump check strainer and strainer plug and gasket assembly.
32. Install pump spring.
33. Install pump plunger and rod assembly.
Fig. 3
Bowl Cover and Pin Ass'y Needle and Seat Ass'y
Bowl Cover Gasket Float Lever Pin
Float and Lever Ass'y
Choker Valve Ass'y
Air Horn Attaching Screw Low Speed Passage Plug and Gasket Ass'y
Bowl Cover Gasket
Body Flange Attaching Screw
Low Speed Jet Ass'y
Idle Well Jet Idle Adjustment Screw
Idle Port Rivet Plug Throttle Valve
Pump Arm and Collar Ass'y
Pump Arm Spring
Metering Rod Pin Her Nut
Metering Rod Pin
Pump Operating Lever Ass'y Nozzle Plug and Gasket Ass'y
Nozzle Metering Rod
Metering Rod Jef and Gasket Ass
Throttle Connector Rod Throttle Shaft Arm and Screw Asi y Spring Retainer
y17
|