Engine Bearings
Fig. 6. Don't relieve, lengthen, or scrape out a built-in oil reservoir
at parting joint. At right (E) mechanic has relieved and lengthened
reservoir which allowed a path of leakage out of ends of bearings.
(C) split edges of half-bearings (incorrect) should touch when
connecting rod and cap are bolted together. (D) note that relief
at split edge does not extend full length of bearing (correct).
(E) oil leakage will result where relief is extended full length
(incorrect).
Fig. 6A. An end view of the path of leakage due to full-length
relief is shown at the left (incorrect). It is not advisable to
relieve the babbitt adjacent to the parting line on a connecting-rod
or main bearing. Too much relief, as shown at the left, is a frequent
cause of oil leakage from the bearing.
00 Afar tat MAIM RCA/OW 0400/T I/OL£ 5101550 14VC NOT MORE
Tail
.002 0451ET2/CAL CL£42AAICC W
200 '6017)
Fig. 7 Fig. 7A
Fig. 7. On all pressure lubricated engines, the bearings are either
of the shimless type and the caps are filed or lapped down, or
closely fitted shims, sometimes of the babbitt tipped type, are
used as in Figs. 7 and 7B in order to prevent oil leakage. Never
remove the babbitt from babbitt tipped shims. A shim that is a
sloppy fit on rod bolt is worthless and should be discarded.
If plain type shims are used, as shown in Fig. 7A, oil will leak
out; if fitted as at left of Fig. 7C, they should be fitted as
shown in Fig. 7C at right.
On splash-lubricated engines, the plain shim can have a much as
1/16" clearance at journal without bad results.
Fig. 7B Fig. 7C
Fig. 7B. This illustration shows a shimmed
bearing of halves each
less than half a circle on a pressure-lubricated engine with the
babbitt-tipped shims properly installed. The edges of shims should
cone within .002" of touching the crank
Fig. 7C. This illustration shows (on the left side) an improperly
fitted babbitt-tipped shim. Too much of the babbitt has been removed,
and the bearing will leak oil.
On the right of this illustration (Fig. 7C) an example of fitting
a plain shim is shown. Note: if plain shims are used they should
be fitted to within .004" or .005" of touching crankpin.
FACTORY METHODS OF FITTING ENGINE BEARINGS
To the maintenance station with limited facilities, the adoption of factory methods
of bearing fitting may not be possible, but the idea in giving this information
is to familiarize the maintenance opera-tors with factory methods, and they can
apply the principles of those methods and that portion of the factory procedure
which is applicable to their individual institution.
The modern methods of factory production, in regard to engine bearings, have
brought about a marked decrease of the use of hand scraping tools.
The hand scraping method of fitting engine hearings is by no means obsolete;
nevertheless the scraping method is either a preliminary or finishing operation,
while the bulk of the work is taken care of through the use of labor-saving tools
and machinery.
In a consideration of the general subject of engine-bearing maintenance, it is
well to keep in mind the units that go to make up a bearing assembly iii the
conventional type of motor vehicle engine. They are:
1. The crankshaft
2. The crankcase
3. The connecting rod and the bearing metal The Crankshaft
The crankshaft on even large production jobs has a close finish of the journals.
The main bearing crankshaft journals' are held to .001" diametrical tolerance.
Because of the necessities of production, and to provide interchangeability,
it is common to reject a crankshaft which is .001" undersize or oversize
of the specified diameter on any one of the crankshaft-bearing journal pins.
Fig. 8. Lapping a crankshaft - bearing journal with a lapping tool. Even new
shafts are lapped at the journals before fitting (see page 791, showing how to
make a lapping-tool)
Crankshaft-bearing journals, and crankpins are lapped (Fig. 8) in addition to
being ground. Al-though grinding was supposed to leave the metal with an apparently
smooth surface, it has been found with microscopic examinations that very small,
yet pronounced irregularities of the surface exist. By lapping, and thus obtaining
a smooth initial finish of the crankshaft journals and crankpins it has been
found that the safe initial clearance between shaft and hearing can be materially
decreased and bearing life noticeably increased.
The widespread trend toward drilled crankshafts providing pressure lubrication
no doubt has been a large factor in the long life now secured from main and connecting-rod
bearings. The efforts on the part of one or two prominent American firms to secure
the maximum engine life has accounted for the use of case-hardened crankpin and
main hearing journals on the crankshafts by these concerns.
In speaking of a journal, this is intended to apply to that part
of the crankshaft where the main bearing halves fit, and the term
crankpin, or crankpin journal applies to that part of the crankshaft
where the connecting rods fit.
Previous page 1927
Supplement Home Next page 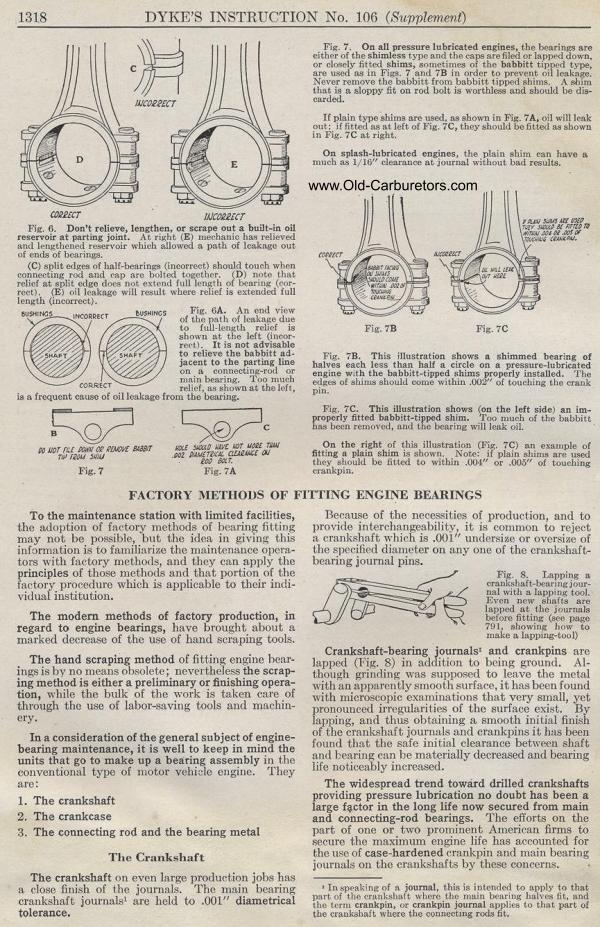 |