Engine Bearings
By holding the dimensional tolerances of the bearings, seats, and
crankshaft to close limits such as .0005 the interchangeable
type of bearing permits replacement of upper or lower bearing
half without any hand fitting whatever.
The methods of manufacture utilized in building the inter-changeable
type bearing to the fine degree of accuracy demanded are controlled
by patents in some cases. Two large bearing manufacturers, the
Federal Mogul Corp. and Bohn Metal Co. supply several car and engine
manufacturers, while a few of the ear manufacturers, such as Marmon
and Oldsmobile, build this type of bearing for their own use in
their own plants.
Fig. 10D. A typical crankshaft main bearing
Oil grooves in bearings have received considerable study in recent
years, and the choice of the majority of the manufacturers has
been concentrated on a few well-worked-out designs which have replaced
the many fantastic and almost useless designs of former years.
Oil grooves are omitted on most pressure systems.
Two types of oil grooves which are widely used are shown in Fig.
11.
Fig. 11. Two easily produced and efficient types of oil grooves
in the bearing halves. The shimless connecting-rod bearing is always
made for pressure lubrication and is usually grooveless.
Efforts to secure permanent anchorage of the bearing halves in
the cap and crankcase have led to the adoption of cast-in or integral
bearings in many cases. Approximately 96 per cent by numbers, of
American passenger car engines use lower connecting-rod bearings
of the cast in babbitt type.
Another method, commonly used to prevent rotation of the bearings,
utilizes shims that are wide enough to exert a pressure on the
bearing half, when the cap is drawn down.
Locking screws which secure the bearing to its seat are also widely
used either without the retaining type of shim or in conjunction
with it.
The S. A. E. standard babbitt metals and certain proprietary combinations
are widely used for the connecting rod and main bearing lining,
and when in doubt as to the most suitable metal, the maintenance
operator will make no mistake in specifying S. A. E. metal.
Bearing Fitting Methods
There are six general methods of bearing fitting used among the
American car and engine manufacturers, as follows:
1. Bore or fly cut, and line ream only, on the main bearings.
Bore, broach' and line ream only on the connecting-rod bearings.
I Broach is a method of bringing to size either a square or circular
orifice by means of a cutting tool of the non-rotating type; for
example, most all connecting-rod lower ends are finished by broaching
at the factory and broaches also are used on piston-pin bushings.
Some of the concerns who make broaching machines or broaches are
J. N. LaPointe Co., New London Conn., The Cutter-Wood Supply Co.,
Boston, Mass., Sheldon Machine Co., Chicago, Ill., Connecticut
Broach and Mch. Co., New London, Conn.
The hand scraper is used only to touch up the ends or fillets of
the rod and crankshaft bearings.
Connecting-rod bearings are given a burnishing operation to impart
final finish.
This method has more adherents among manufacturers than any of
the other five methods conunonly used. It is used by five of the
large engine companies, including such firms as Buda, Continental,
Falls, Waukesha, and Wisconsin. Of the 16 car manufacturers, whose
bearings are fitted in this manner, 4 are in the over $4,000 class.
2. Bore or fly cut and line ream, followed by hand scraping for
surface finish on the main bearings.
Bore or broach, ream, and finish surface by hand scraping on connecting
rods.
Three of the firms which manufacture their own engines and use
this method are in the over $4,000 class.
One engine manufacturer is included in the list of 13 adherents
to this method.
3. Bore, or fly cut, followed by hand scraping, no line reamer
being used on the main bearings.
Bore or broach followed by hand scraping only, on the connecting
rod bearings.
Two car manufacturers and one engine manufacturer are listed as
using this method.
4. Main and crankshaft bearing holes with caps installed are rough
bored, then semi-finished bored, leaving about .008 for finishing
cut, which is done with single point tool having a diamond insert.
Bearing shells are installed in finished holes (no liners or shims
being used) in cap and case.
Caps are bolted down, and are finished cut by same process using
single point diamond insert tool.
The same method is followed with the connecting rods except that
the rod holes or bearing seats are ground to a specified diameter
instead of being bored; the joint faces of rod and cap are then
lapped to form the joint.
The bearing halves are inserted and finished in a fixture with
a single-point diamond insert tool.
Two car manufacturers, both in the over $3,000 class, use this
method. Very similar to method No. 5. Bearings may be replaced
in the field without hand fitting.
5. A method which combines some of the features of the four methods
mentioned, except that the hand scraper is not used on the bearings
themselves, al-though the bearing seats are sometimes hand scraped.
The first operations consist in preparing the seats or holes in
the case and lower end of connecting rods.
It is necessary that the case and rod holes be accurately finished,
and for that reason several different methods are being used at
present.
The holes or seats for bearings are either bored, line reamed,
fly cut, or ground.
Some firms line-ream and hand scrape the case holes; another firm
grinds these holes, and a third manufacturer uses the single-point
diamond insert tool.
The bearings are made by a special method and are held to very
close tolerances, especially the inside and outside diameters.
After the case holes have been finish-machined, the bearings are
installed and the crankshaft is bolted down permanently.
The bearing halves that permit this method of bearing fitting are
of what is known as the inter-changeable type. It is said that
replacement of this type of bearing in service work is accomplished
Previous page 1927
Supplement Home Next page 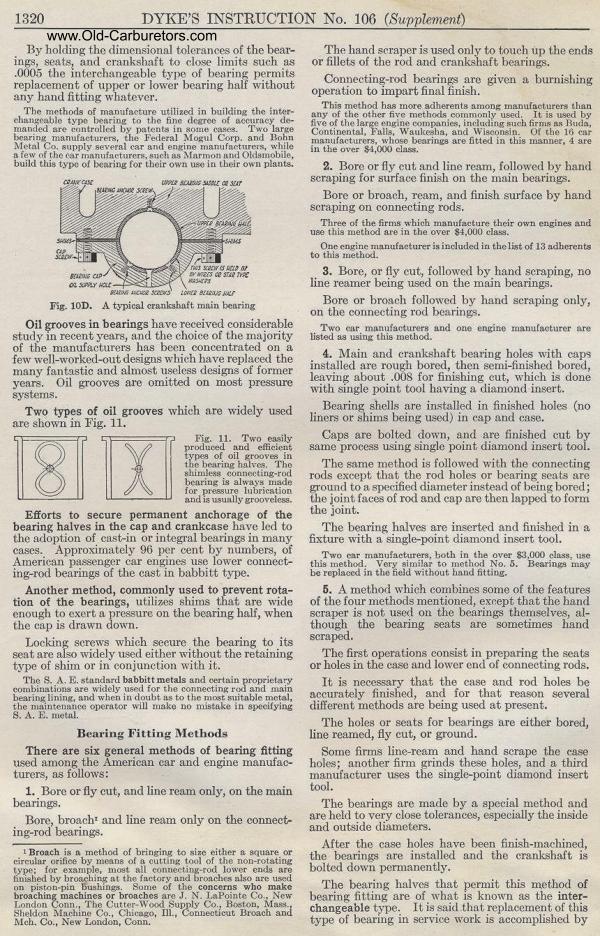 |